Flex PCB – Innovative, Lightweight, and Reliable
At MultPCB, our Flex PCBs offer cutting-edge solutions for applications that demand flexibility, reduced form factor, and exceptional performance. Designed with precision and manufactured using advanced techniques, our Flex PCBs are ideal for wearable devices, flexible displays, and other next-generation electronics.
What Is a Flex PCB?
Flex PCBs (Flexible Printed Circuit Boards, usually short for FPC or FPCB) are designed on flexible substrates, allowing them to bend, twist, and conform to various shapes. They offer significant advantages over rigid boards by enabling compact, lightweight, and innovative designs while maintaining excellent electrical performance. Key Features of FPC including:
High Flexibility & Durability:
Our Flex PCBs are manufactured using high-quality polyimide or other flexible materials that ensure reliable performance even under repeated bending and stress.Thin and Lightweight:
Optimized for space-constrained applications, our Flex PCBs minimize board thickness and weight without compromising functionality.High-Density Interconnects:
Designed for advanced applications, our boards support fine line widths and high-speed signal integrity.Robust Adhesion and Bonding:
Our manufacturing processes ensure strong adhesion between layers, providing long-lasting mechanical and electrical stability.Customizable Designs:
Whether you need a single-sided or double-sided flex board, our team works closely with you to customize the layout, layer configuration, and material specifications.- Rigorous Testing & Quality Control: Each board undergoes a series of mechanical bending tests, automated optical inspections (AOI), and electrical continuity tests to guarantee top quality.
MultPCB Flex PCB Capabilities
Our state-of-the-art manufacturing facilities enable us to offer the following capabilities:
Feature | Specification |
Substrate Material | High-quality polyimide (PI) |
Layer Count | 1 to 8 layers (customizable to meet project requirements) |
Board Thickness | 0.08 mm to 0.5 mm |
Maximum PCB Size | 2000mm*240mm for 1-layer, 800*240mm for 2-layer, 350*240mm for multilayer FPC |
Copper Weight | 0.5oz, 1oz, 1.5oz, 2oz (customizable based on current and thermal requirements) |
Minimum Trace/Spacing | As fine as 3 mil / 3 mil for high-density layouts |
Stiffener Materials | Polyimide, FR4, Stainless Steel, Aluminum |
Surface Finish Options | Organic Solderability Preservative (OSP), Electroless Nickel Immersion Gold (ENIG), Immersion Silver, Immersion Tin |
Coverlay Options | Yellow, White, Black, Clear |
Testing Methods | Automated Optical Inspection (AOI), Electrical Testing (Flying Probe/E-test), and Mechanical Bending Tests |
Lead Time | Prototypes: 3–5 days; Standard production: 5–7 days; Volume orders: 8–15 days (depending on complexity and quantity) |
Certifications | Conforms to IPC standards, ensuring reliability and performance for high-end applications |
Standard FPC Stack-up Structure
A stack-up refers to the arrangement of layers—conductive, insulating, and protective—in a flexible printed circuit. The stack-up determines the electrical performance, mechanical flexibility, and manufacturability of the circuit.
Standard 1-layer FPC Stack-up Structure
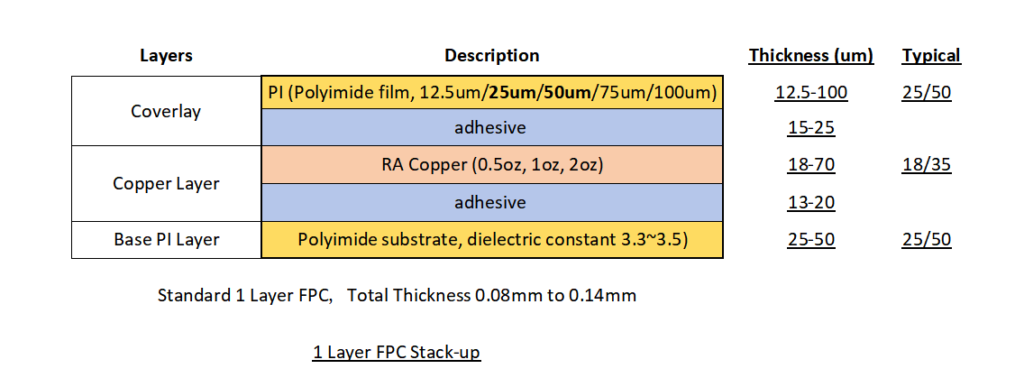
Standard 2-layer FPC Stack-up Structure
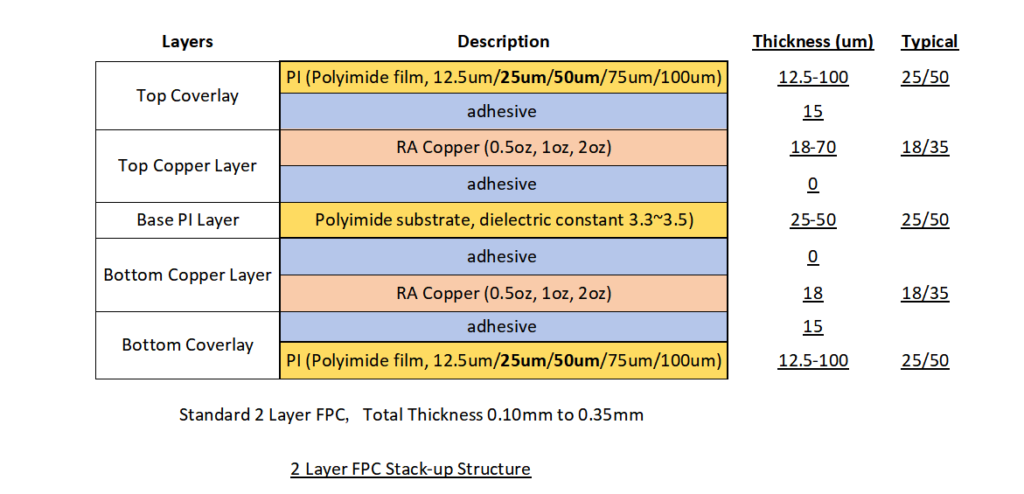
Standard 4-layer FPC Stack-up Structure
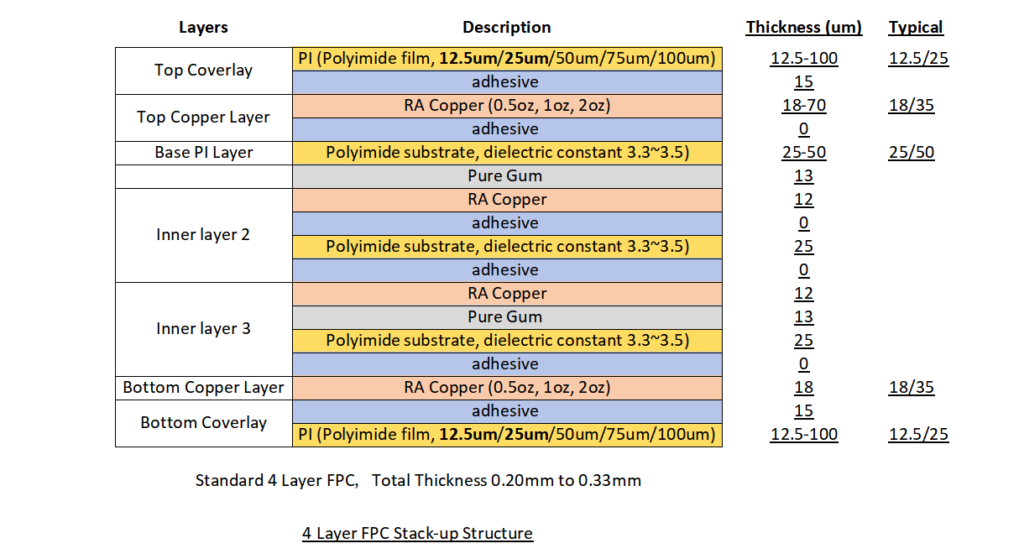
Standard 6-layer FPC Stack-up Structure
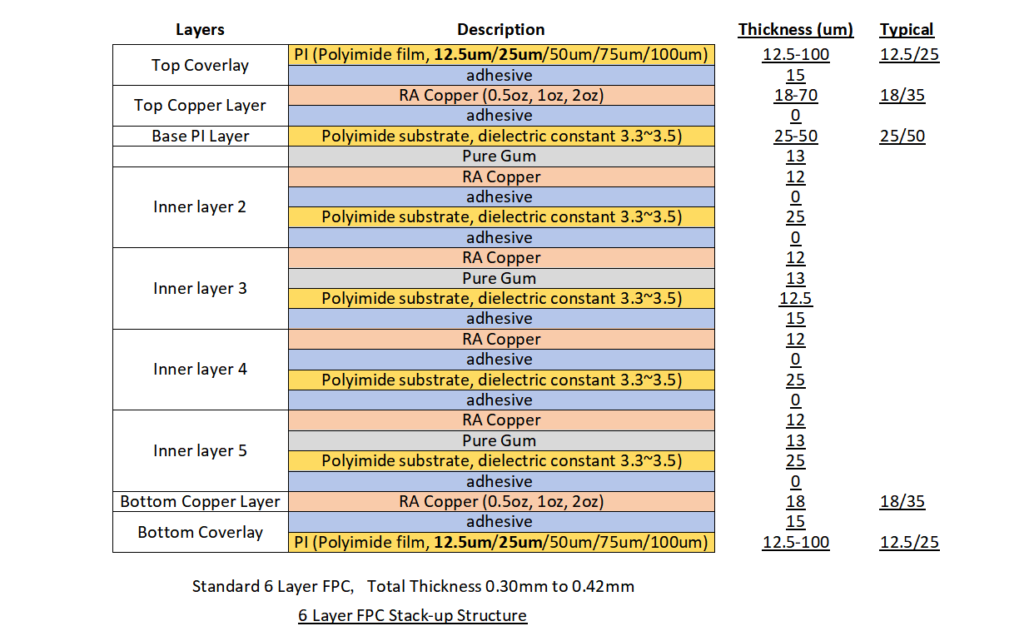
Materials Used in Standard Stack-ups
Material | Type | Notes |
---|---|---|
Base Film | Polyimide (PI) | High flexibility, excellent thermal & chemical resistance |
Copper Foil | RA Copper | Rolled Annealed preferred for dynamic bending |
Adhesive | Epoxy / Acrylic | Bonds copper to PI or coverlay layers |
Coverlay | PI + Adhesive | Replaces traditional solder mask, protects traces |
How to Produce A Flex PCB? --Detail Process
Below is a table outlining the typical production process for Flex PCBs:
Step | Description |
1. Design & DFM Review | Collaborate with our engineering team to create a flexible PCB layout using advanced design software, followed by thorough Design for Manufacturability (DFM) checks to optimize the design. |
2. Material Preparation | Select high-quality flexible substrates (e.g., polyimide) and prepare copper foils. Materials are pre-treated to ensure proper adhesion and performance in a flex environment. |
3. Imaging & Etching | Transfer the circuit pattern onto the flexible substrate using high-resolution photolithography with photosensitive dry films and UV exposure. Then, chemically etch away unwanted copper. |
4. Lamination (for Rigid-Flex) | For rigid-flex applications, bond flexible layers with rigid sections using controlled heat and pressure to form a unified board, ensuring precise layer alignment and robust adhesion. |
5. Drilling & Via Formation | Use computer-controlled drilling systems to create fine vias and holes (often around 0.2 mm), and plate them to establish reliable electrical connections between layers. |
6. Coverlay Application | Apply a high-quality coverlay film to protect the flexible circuitry. This coverlay provides additional insulation and mechanical protection while maintaining flexibility. |
7. Surface Finishing | Apply desired surface finishes such as OSP, ENIG, Immersion Silver, or Immersion Tin to enhance solderability, protect copper traces from oxidation, and meet application-specific requirements. |
8. Final Inspection & Testing | Conduct rigorous quality control, including Automated Optical Inspection (AOI), electrical continuity tests (e.g., flying probe or E-test), and mechanical bending tests to ensure reliability. |
9. Packaging & Shipping | Package the finished Flex PCBs securely to prevent damage during transit and ship them according to customer requirements. |
This structured process ensures that our Flex PCBs meet high-performance standards and are produced reliably for a wide range of applications.
Applications of Flex PCBs
MultPCB’s Flex PCBs are versatile and find use in a variety of cutting-edge applications:
Wearable Electronics: Ideal for smartwatches, fitness bands, and health-monitoring devices.
Flexible Displays: Critical for foldable phones, tablets, and advanced display technologies.
Medical Devices: Used in portable diagnostic equipment and implantable devices requiring conformal circuits.
Automotive Electronics: Implemented in instrument clusters and infotainment systems that benefit from flexible design layouts.
Consumer Electronics: Enhance compact designs for cameras, audio devices, and other modern gadgets.
Industrial & IoT Devices: Offer adaptable circuit solutions for sensors, smart packaging, and control systems.
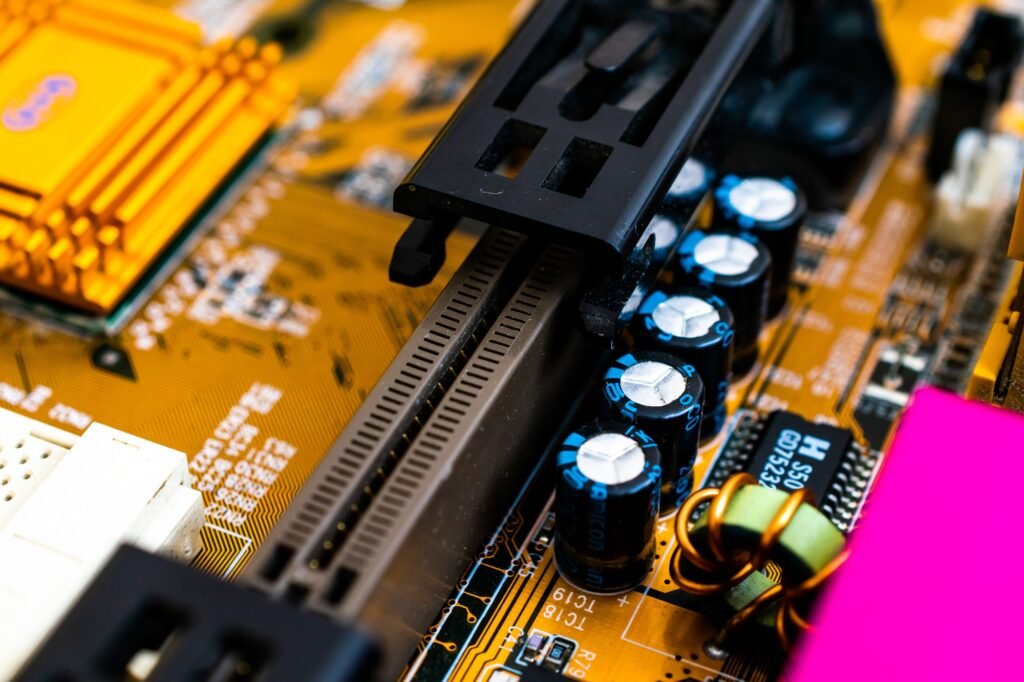
Why Choose MultPCB for Your Flex PCB Needs?
Expert Engineering Support:
Our experienced team assists you through each step of design and production, optimizing your layout and material selection for best performance.State-of-the-Art Manufacturing:
We leverage advanced equipment and controlled processes to produce Flex PCBs that consistently meet international quality standards.Customization and Flexibility:
Our flexible solutions are fully customizable to your specific application requirements, whether for single-layer, multilayer, or rigid-flex boards.Fast Turnaround and Competitive Pricing:
Benefit from our efficient production processes that balance speed, cost, and quality—ideal for both prototypes and large-volume orders.Global Quality Assurance:
All our products adhere to IPC standards and other international certifications, ensuring reliable performance across diverse applications.